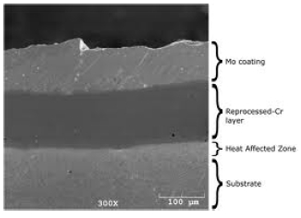
Overview – Molybdenum is metal layer that is regularly used as a back contact layer for inorganic thin film solar cells, such as CIGS and CdTe. The most common method used to deposit Molybdenum is sputtering, especially in high volume manufacturing environments. The advantages of a sputtered process include precise process control with scalable processes while still maintaining the ability to tune molybdenum layer properties for structure optimization. Reactive sputtering of molybdenum oxide has also been used as a buffer layer to improve the efficiency of thin film organic solar cells
Challenges – Molybdenum deposition can appear simple when compared to the complex deposition of CIGS. However it is important not to trivialize the importance of properly controlling and optimizing the molybdenum layer. For CIGS cells, molybdenum forms the foundation for the solar cell layer stack and will influence doping (intentional doping or impurity diffusion), CIGS grain size, adhesion, and surface roughness. Similar challenges are encountered for substrate deposition of molybdenum for flexible CdTe cells. Improper molybdenum deposition parameters will damage the CdTe absorber when using traditional superstrate deposition on glass.
A single molybdenum recipe is not ideal for all layer structures.